Cleanliness requirements. What can we do for you?
Cleanliness requirements GRADE-2 (also known as GRADE-2 cleanliness) is a standard, specified differently by every producer, to describe the cleanliness requirements upon the delivery of vacuum products.
In the GRADE-2 Cleanliness guidelines, the maximum number of dust particles is described that are allowed to be found on the surface of the end product. The GRADE-2-guidelines also make clear what the maximum degassing percentage can be in a vacuum. Different types of steel must comply with the criterium of the low degassing; for instance, with products, for high or ultra-high vacuum applications. The degassing is measured by a Residual Gas Analysing meter (RGA; residual gas analysis). The degassing percentage is defined in water (H2O) and in volatile and non-volatile hydrocarbons.
Any questions about cleanliness requirements?
Do you have any questions about cleanliness requirements, such as GRADE 2-Cleanliness, and about what Nefratech EDM-Center could do for you in this regard? Then contact Frank Lenaers (manager) or Sven Stoffelen (general manager production).
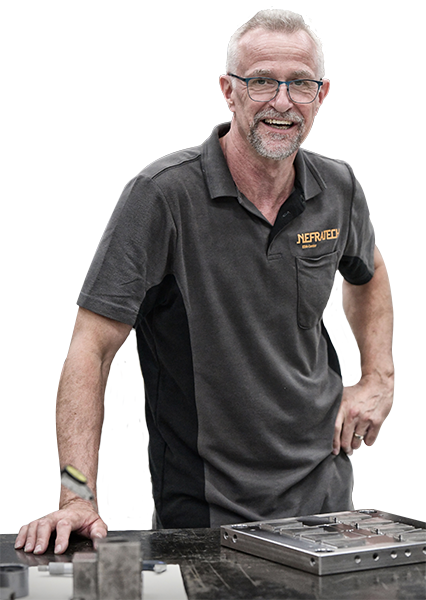
What can you expect from Nefratech EDM-Center?
You can expect us to be dedicated to producing and delivering products in accordance with your specifically provided cleanliness requirements for manufacturing, assembly, as well as packaging.
General guidelines
During all actions throughout the production process, the assembly, and the packaging, all kinds of pollution are being avoided. Employees will be wearing synthetic gloves to prevent fingerprints. After every action, the gloves will be replaced.
The machines and all tools used must be free from foreign materials/metals before a new production process is started.
Residue deriving from previous productions must be removed before a new product is started. Residue deriving from the production process (fluids and metal parts) must be removed immediately in between the process stages.
Intermediate cleaning must be performed as quickly as possible (wet-in-wet) and after every production step, in order to prevent dirt drying up and/or contaminating. Machines are cleaned by the use of special agents and clean water. Drying is done by use of N2 or clean, oil-free Clean Dry Air (CDA).
The machine is maintained with refrigerants and lubricants with a low PH value. A high PH-value will quickly corrode the product surface and must therefore be removed immediately by means of rinsing with water.
Maintenance products must be free of sulfur and silicones. No traces of machine fluids may be detected during the last stage via RGA (Residual Gas Analysis). Neither of the maximum lifespans and temperatures of the fluids may be exceeded.
Fluids must be refreshed frequently in order to remove agents/components that were not solved from the fluid. Machine oil may not end up in the refrigerant.